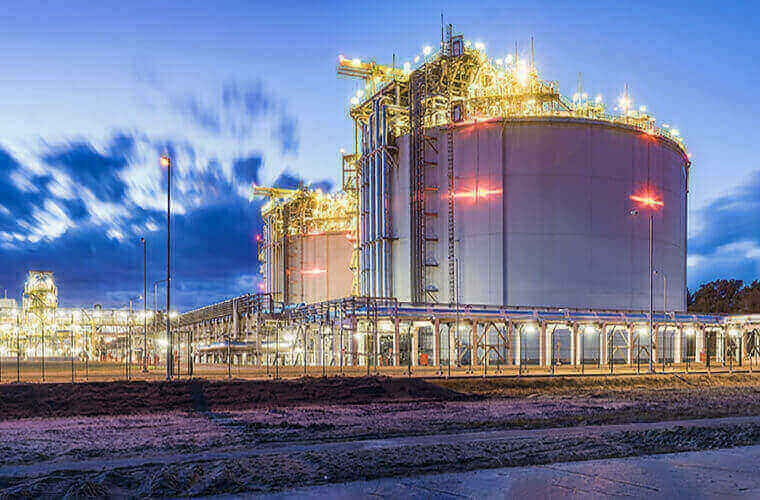
Suspended Deck For LNG Tanks
Every year more and more natural gas reserves are discovered. Unfortunately, much of it is found far from the major consumer countries making economical transportation and distribution vital. The only practical method of transporting this gas is to store and transport it at cryogenic temperatures (-265°F or -165°C) which liquefy the gas reducing its volume by a factor of 600:1.
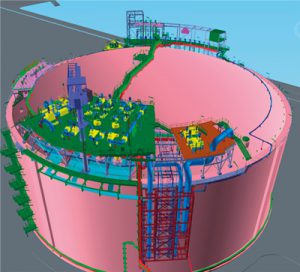
It has become common practice to provide tanks containing low temperature or cryogenic liquids with a suspended deck that supports a layer of insulation above the high liquid level. These decks must be durable to support the insulation and installation workmen and must be of a material suitable for the cryogenic temperatures encountered in this service. Several materials are suited for cryogenic temperature applications, notably aluminum, stainless steel, and 9% nickel steel, but these materials are expensive and more difficult to weld under field conditions.
The CRYODECK™ Suspended Aluminum Deck is assembled without welding using aluminum mechanical locking fasteners (Huck Bolts). The deck loads are supported by a stressed membrane design. The CRYODECK™ can be easily and quickly assembled in the field using inexperienced workmen and without expensive erection equipment.
Since these cryogenic LNG storage tanks typically require a deck around 250 feet (76.2 meters) in diameter +/-, quick and simple assembly with the fewest number of parts becomes very important. The CRYODECK™ assembly schedule removes the deck assembly from the critical path of most project schedules.
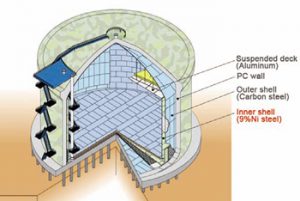
The CRYODECK™ design uses proven technology from both the ATECODECK Internal Floating Roofs and ATECODOME™ Aluminum Geodesic Domes. The basic deck structure consists of three sets of clamp beams, similar to those used on our floating roofs, but with larger flanges. Each of these clamp beams are designed to “nest” inside the next so that the flanges can be easily fastened together. Since the most common design for the outer steel roof of these storage tanks is a dome roof supported by a number of radial rafters,
the CRYODECK™ design consists of radial clamp beams which are aligned directly under the radial outer roof rafters. Cross clamp beams which fit inside of the radial clamp beam flanges go across from radial clamp beam to radial clamp beam. Around the outer edge of the deck is a rim clamp beam that fits outside the flanges of the radial clamp beams. This allows the peripheral closure plates to be easily attached.
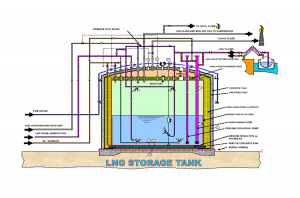
Deck panels, made out of 0.050” (1.27 mm) thick aluminum, are shop cut, both dimensionally and with fastener holes. When all of the clamp beams are assembled above and below the lapped edges of these panels, they form a “membrane” that supports the insulation loads and workman loadings in almost pure tension making them very strong for their weight. The “grip” of the clamp beams along these lapped edges, which is identical to the “grip” we have been using on floating roofs for more than 35 years, is vital to the overall strength of the deck.
The deck is “hung” from the outer dome roof rafters on a large number of 5/16” diameter stainless steel cables. The exact number will vary depending on the design loadings required on the project and the “pattern” of the rafters. 700 to 800 cables are common. A typical construction method is to build these large diameter dome roofs near the tank floor and “air raise” the roof into place. This is a technique well known to most companies in the tank industry. The preferred construction method is to build the suspended deck under the outer dome roof before it has been air-raised. The door sheet is open at this time. The deck will later go up with the outer roof.
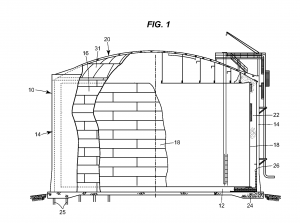
Since the steel dome roof cannot be lifted until our deck is completed, the speed of the deck assembly becomes even more critical than just the cost of the field labor. For this reason, the design has everything pre-punched, pre-drilled, pre-cut, etc. to allow rapid assembly of the deck.
After the outer steel dome roof and suspended deck have been air raised into place, the inner storage tank must be constructed. The inner tank is usually made out of 9% nickel steel and is positioned five (1.524 meters) or six feet (1.8288 maters) inside the outer tank to leave room for insulation. In order to have room to lift and weld this tank, the deck is usually several feet smaller in diameter than this inner tank. How much smaller varies with the tank builder.
After the inner tank is finished, the “gap” between the deck and the top of the inner tank must be closed. Since the inner tank is 9% nickel steel and the deck is aluminum, they will shrink at different rates when they are cooled down to –265°F (-165° C). This means the “closure” pieces must be able to move relative to the top of the inner shell as much as six inches (152.4 mm) or more. The closure pieces are stiffened panels, designed to support the insulation and workmen across the gap. The inside edge is fastened to the rim clamp beam flanges and the outer edge rests on the top edge of the inner tank shell. The closure pieces usually have a down – turned lip of 6” (152.4 mm) which is 10” (254 mm) outside the inner shell in the warm condition.
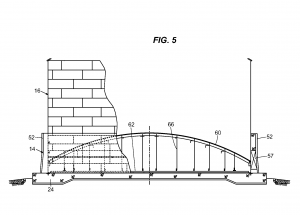
The closure pieces cover the top edges of fiberglass insulation batts which are attached to the outside surface of the inner tank. These fiberglass battens help control the compaction of the loose fill Perlite. Loose fill Perlite is placed in the annular space between the inner and outer tanks. Because of long term compaction of the Perlite, a Perlite reservoir is added above the annular space. The suspended deck is designed at the outer edge to handle the additional load from the Perlite reservoir. It is important that the deck be designed and installed such that Perlite does not migrate into the inner tank. Perlite can damage the in-tank LNG pumps.
The number of roof rafters will vary from tank builder to tank builder.The number and “pattern” of our clamp beams and panels will be varied to match the roof pattern.
The suspended deck has a large number of penetrations.The penetrations on an CRYODECK™ are square rather than round. The penetration boxes have covers with cut-out holes to match the pipe penetrations.
If permanent platforms or walkways are required, these are best hung from the roof with the same cable system that supports the deck.
Why does suspended deck need in cryogenic tank?